
n mid-March 2020, just as COVID-19 stay-at-home orders began taking effect in the United States, toilet paper began to disappear. Media reports showed images of decimated supermarket shelves. People alerted friends and family members when they discovered a store with stock. Retailers implemented purchase limits.
In some ways, the panic-buying was similar to consumer purchasing behaviors ahead of hurricanes and winter storms. History has shown that when we might be stuck at home, toilet paper is one of the items we don’t want to be without.
This particular case, however, was different. As people began hoarding at unprecedented rates, retailers — who typically keep just a few weeks of supplies in warehouses, based on years of consistent data — quickly depleted their stock. Manufacturers also had to shift their balance of production, which is typically split between packages of softer, smaller rolls intended for home use and large rolls of thin, single-ply paper used in public restrooms (see Toilet paper tipping point on p. 13).
Toilet paper wasn’t the only product that experienced a disruption.
Working and learning from home led to increased purchases of office furniture and equipment. We invested in our homes with renovations and additions, updated appliances, and pools. We realized new interests like making bread and riding bikes that suited our socially distanced world. Hand soap, sanitizer, disinfectant wipes and cleaners, and personal protective equipment became critical necessities.
As the pandemic raged on, these products and many more experienced both surges and shortages. At the same time, semiconductor shortages, a devastating winter storm in Texas, a factory fire in Japan, ransomware attacks, and a container ship stuck in the Suez Canal continued to hammer the global supply chain.
With so many factors affecting our access to goods and services, all eyes turned to an aspect of production that has historically operated quietly in the background: supply chain management.
In the W. P. Carey Department of Supply Chain Management, undergraduate and graduate students have long been focused on how to maintain and optimize supply chain performance. Alumni studied global logistics networks, data analytics and decision-making, operations, and management strategies, but nothing prepared them for the level of disruption they witnessed in the past year.
Here, W. P. Carey alumni and faculty talk about how the COVID-19 pandemic changed their perspectives on supply chain management, how they pivoted their businesses to respond, and how they’re preparing for the next big disruption.
To say that Lynn Torrel (MBA ’10) has a massive role at Flex would be an understatement.
The company is one of the world’s largest global electronics manufacturers and supply chain providers. Flex helps more than 1,000 customers design and build products, leveraging 100 manufacturing facilities in 30 countries and more than 16,000 suppliers that provide over a million individual parts. As chief procurement and supply chain officer, Torrel manages more than $20 billion in spending across direct and indirect materials, freight and logistics, inventory management, and supply chain solutions.
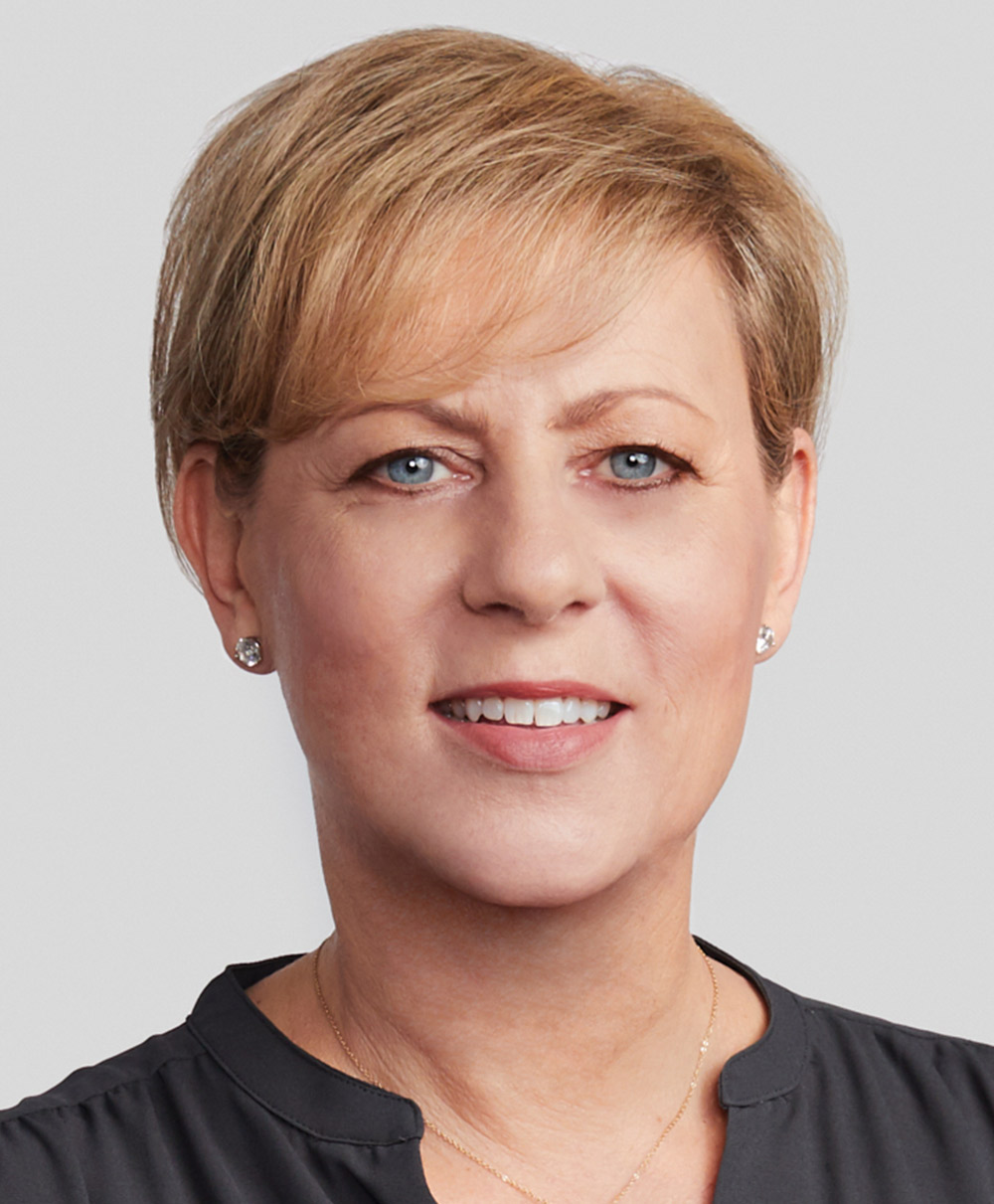
Real-time data, supply chain visualization, and predictive analytics were crucial to anyone monitoring the constantly changing landscape. In this area, Flex was ahead of the curve.
The company introduced its Pulse system in 2015 and now has nine data visualization centers worldwide, each equipped with touchscreen walls pulling up-to-the-minute supply chain data. In addition, a desktop app and specific dashboards help 10,000 supply chain professionals spot coming disruptions and pivot as needed.
“If someone calls me about a shortage, I can go into the tool, identify which customers of which part, which person on my team around the world might have had the last communication, and what was said,” Torrel says. “We’ve been continuously looking at our tools and how we can potentially innovate and use predictive analytics and artificial intelligence to get more intuitive.”
A supply chain disruption can be a matter of life and death for health care companies.
Medtronic, the world’s largest medical device technology company, produces cardiac devices, insulin pumps, surgical tools, patient monitoring systems, ventilators, and a variety of other medical devices and technologies for patients and health care facilities in approximately 160 countries.
As vice president of the Americas Supply Chain, Gaurav Puri (BS Supply Chain Management ’99, MBA ’05) is responsible for planning, distribution, transportation, service and repair, and trade operations for Medtronic’s Americas region. Before the pandemic, one of Puri’s priorities was optimizing the customer experience, from order fulfillment to distribution and delivery. His team was also working closely with transportation partners to pilot new tracking systems that could provide real-time visibility anywhere in the world.
But transportation turned out to be one of the company’s biggest challenges at the onset of the pandemic.
Medtronic was largely dependent on passenger planes to ship products to international markets. When people stopped traveling for business and vacation, the airline industry came to a standstill and the company’s transportation capacity was heavily diminished. This put Medtronic at risk of not being able to continuously fulfill its core mission to alleviate pain, restore health, and extend life.
While Medtronic monitored its transportation channels, Jami Bliss (BS Supply Chain Management ’05), vice president of regional and local procurement at the pharmaceutical company GlaxoSmithKline, watched as raw material suppliers were affected when the virus first started spreading through Asia. Then, as stay-at-home orders hit Western countries, consumers began stocking up on over-the-counter medications and supplements including Advil, Theraflu, and vitamins.
“The first impact for us was supply continuity — making sure we had the raw materials to produce the pharmaceutical and consumer goods, especially for critical and life-saving medicines,” Bliss says. “Supply disruption in the pharma industry means much more than a loss of profit. It means an impact to a patient at the end of the supply chain.”
Dual sourcing was already central to Bliss’ approach, but the pandemic revealed an additional layer to consider.
“Whether it’s a border closure or an environmental impact like a tsunami, if all of your suppliers are within one region, it doesn’t matter if you have three, five, or 10 suppliers,” she says. “If that country or region is impacted, all of your risk-mitigation efforts may still mean you have supply constraints.”
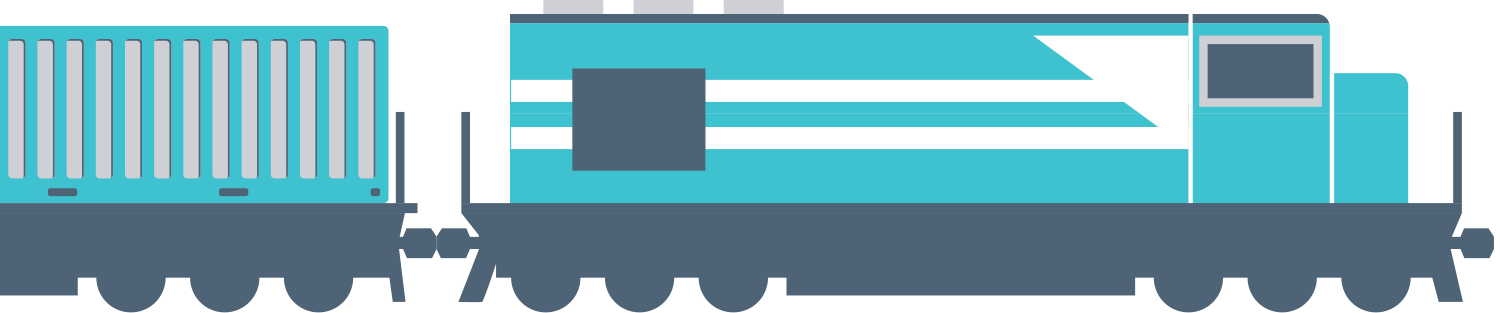
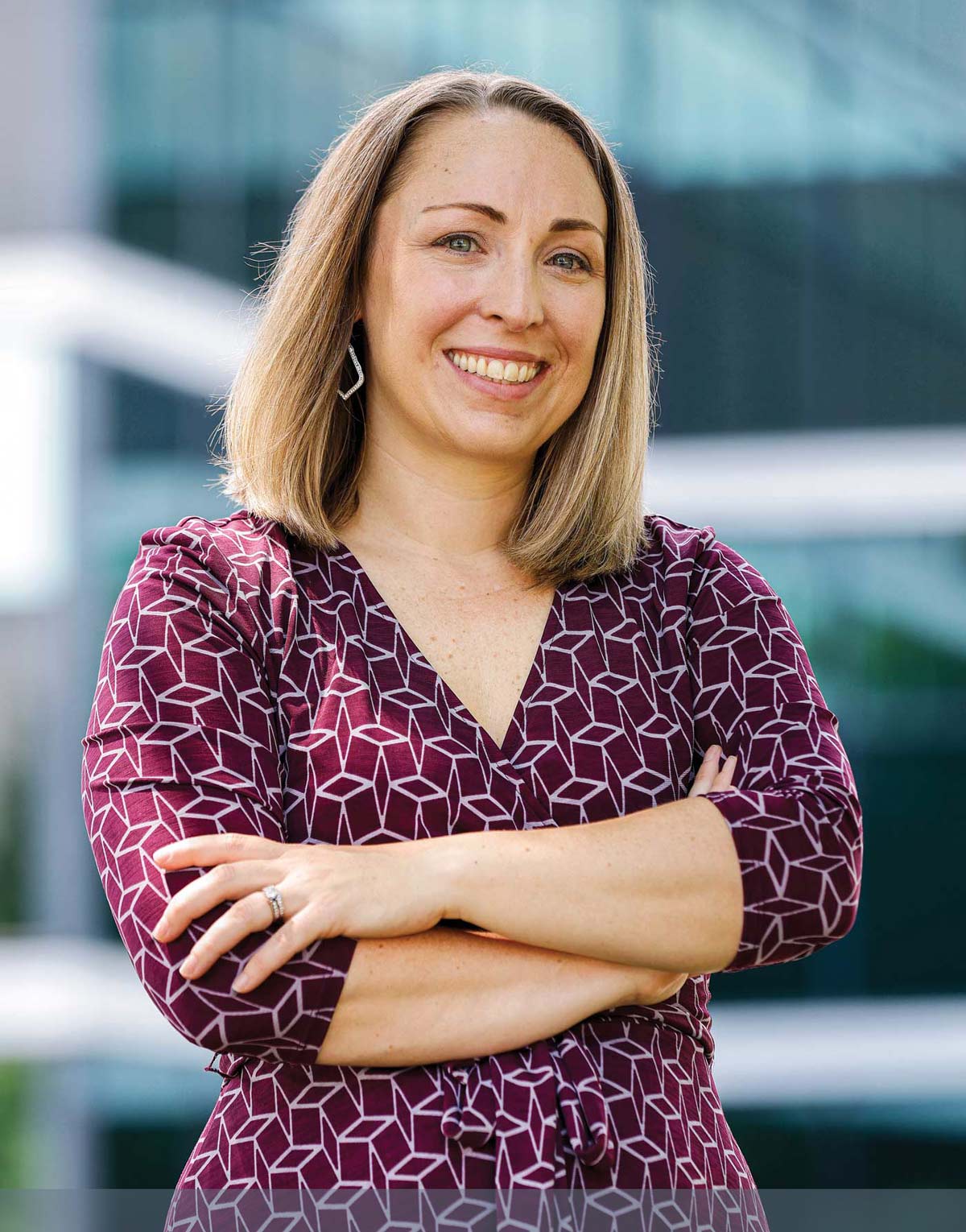
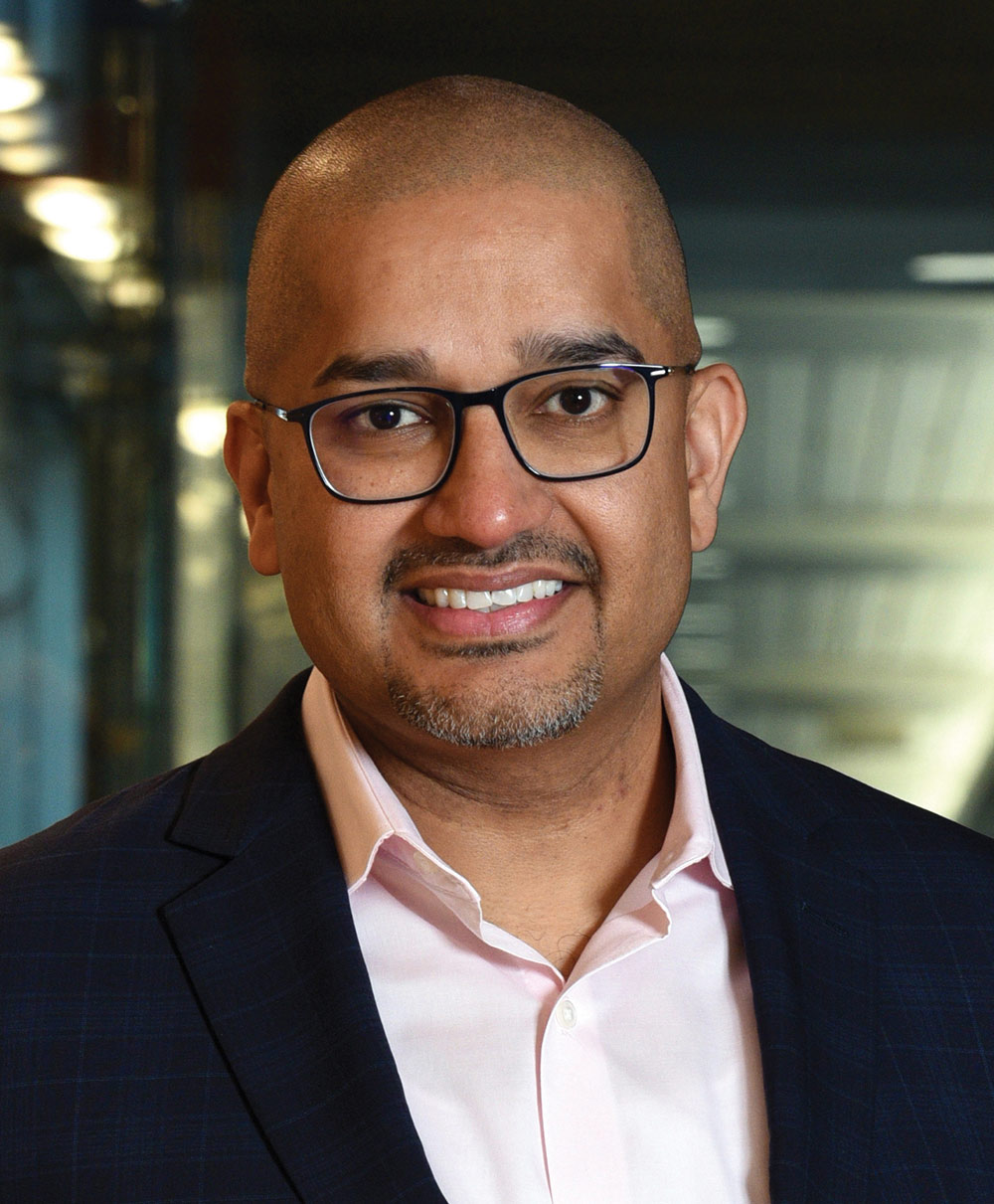
Puri says Medtronic, as part of its standard business continuity planning, identified the most critical products for patient care, then ensured it had alternative suppliers, manufacturing sites, distribution networks, and transportation partners. It also had to ensure that secondary products that enable health care delivery, such as gloves and masks, were adequately supplied.
“COVID-19 reinforced some of our business continuity strategies about, in simple terms, not putting all your eggs in one basket,” Puri says. “Where you place your distribution centers, where you place your manufacturing sites, and who you select as your strategic partners — all have lasting consequences.
“There’s a huge med tech manufacturing presence in Puerto Rico, which is on a hurricane belt. Firms with a presence there need to determine if they need to dual-source certain things and plan for scenarios and actions so that when an event happens, we minimize the disruption and its impact. Our ability to do that with critical products, and to pivot and scale up our operations in other parts of the world, are what enabled us to consistently deliver seamless business continuity to our customers globally.”
Throughout the pandemic, different interests took hold and related product purchases surged as a result. For instance, with extra time at home, people experienced a renewed interest in baking, particularly bread. In March and April, yeast sales jumped more than 400% and, soon after, both yeast and flour were in short supply.
Other categories, like shelf-stable and frozen foods, experienced more predictable increases as people trended toward stockpiling.
To help his clients meet the shifting spikes in demand, Arnold Kogan (BS Finance/Supply Chain Management ’03), managing director and partner at Boston Consulting Group, focused on narrowing product selection based on consumer demand as well as manufacturability.
“If we had five or more flavors of a particular beverage category, for instance, we would simplify that to two,” Kogan says. “If we had different pack formats, we would consolidate those pack sizes.
“We did that based on the manufacturability, which means that we want to run the products that give us the maximum efficiency on the production line, so we can pump out more supply to meet demand.”
Now, Kogan is helping the company with the next stage of simplification through large-capital projects and restructuring. This kind of restructuring is common every five to 10 years as companies acquire production facilities and distribution centers. The recent surge in revenue put many of BCG’s clients in a position to restructure.
Consolidation doesn’t just benefit a company’s bottom line; the process also makes supply chains easier to run.
“We want to considerably consolidate and simplify. We want to automate, to be able to drive speed to our customer base,” Kogan says. “By doing that in a world where demand volatility is increasing, if we have another event where there’s a spike in sales, we have a simplified physical supply chain, a physical structure that has automation that can fulfill at speed and at scale to meet that surge.”
Corteva Agriscience was just establishing its footing as a new company when the pandemic hit. The agriculture company, which began as a division of DowDuPont, officially spun off into a standalone company in mid-2019.
Craig Reed (MBA ’02), vice president and chief procurement officer, says the company’s early days were focused on rightsizing and integrating processes and systems.
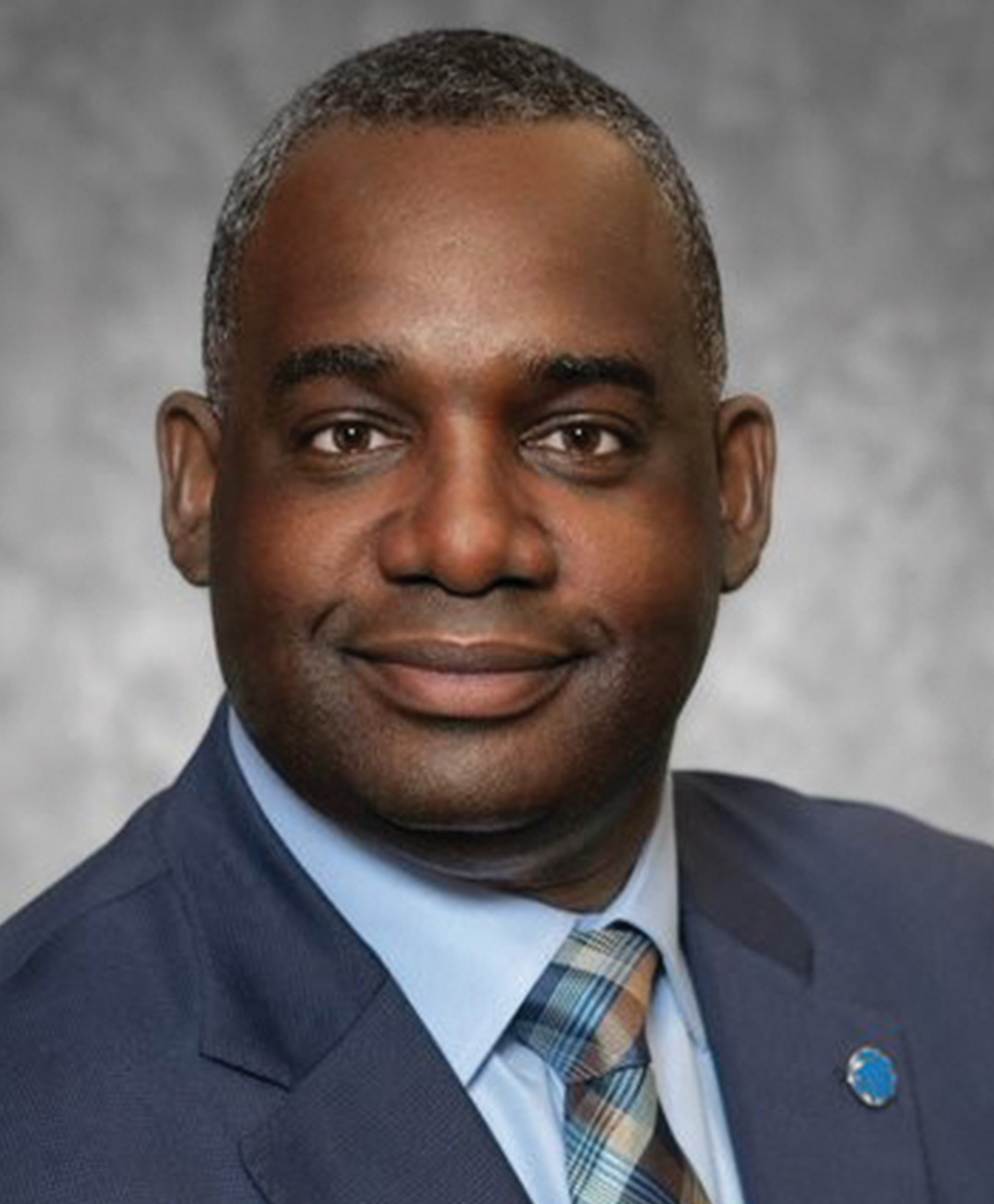
Craig Reed (MBA ’02)
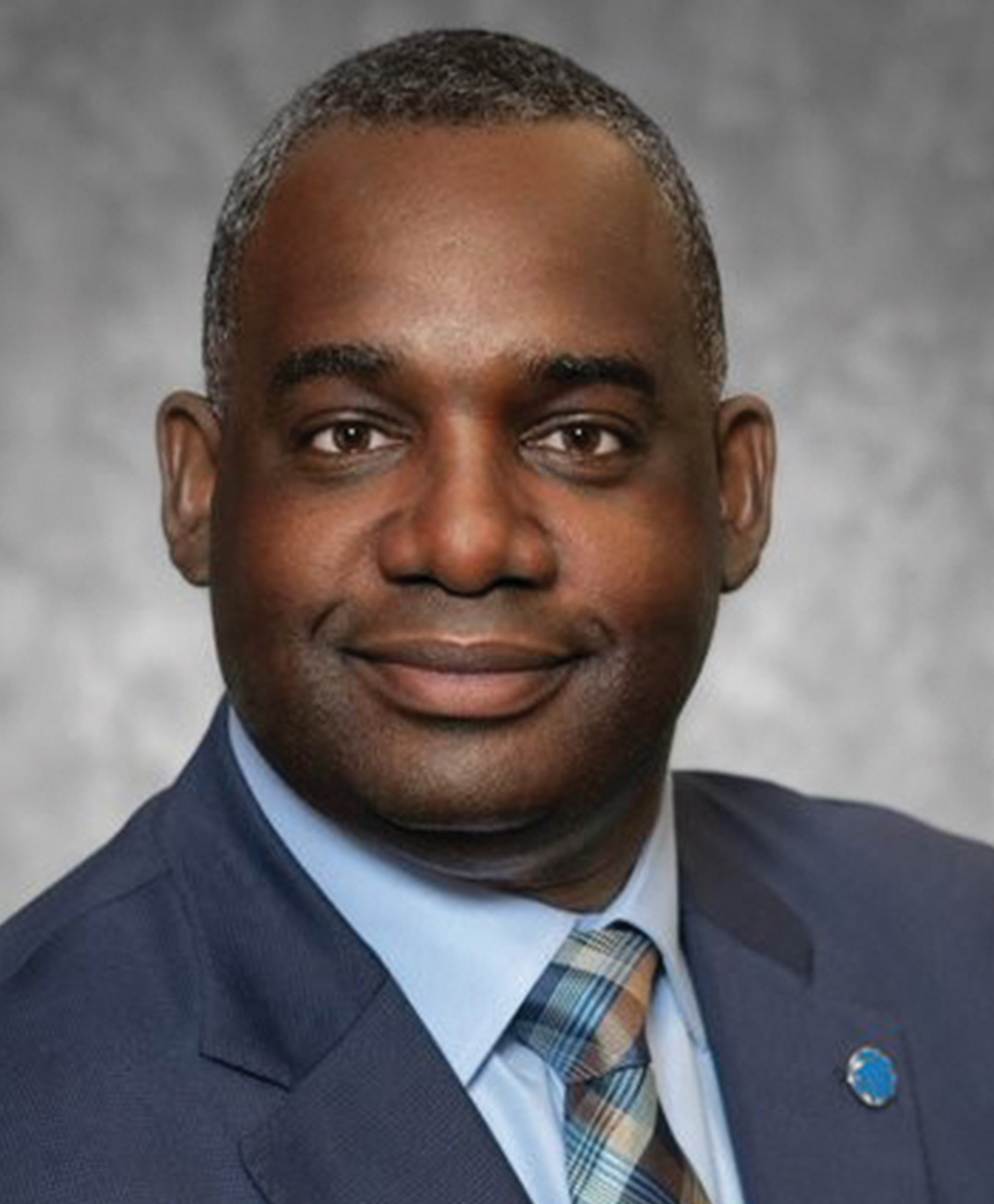
Craig Reed (MBA ’02)
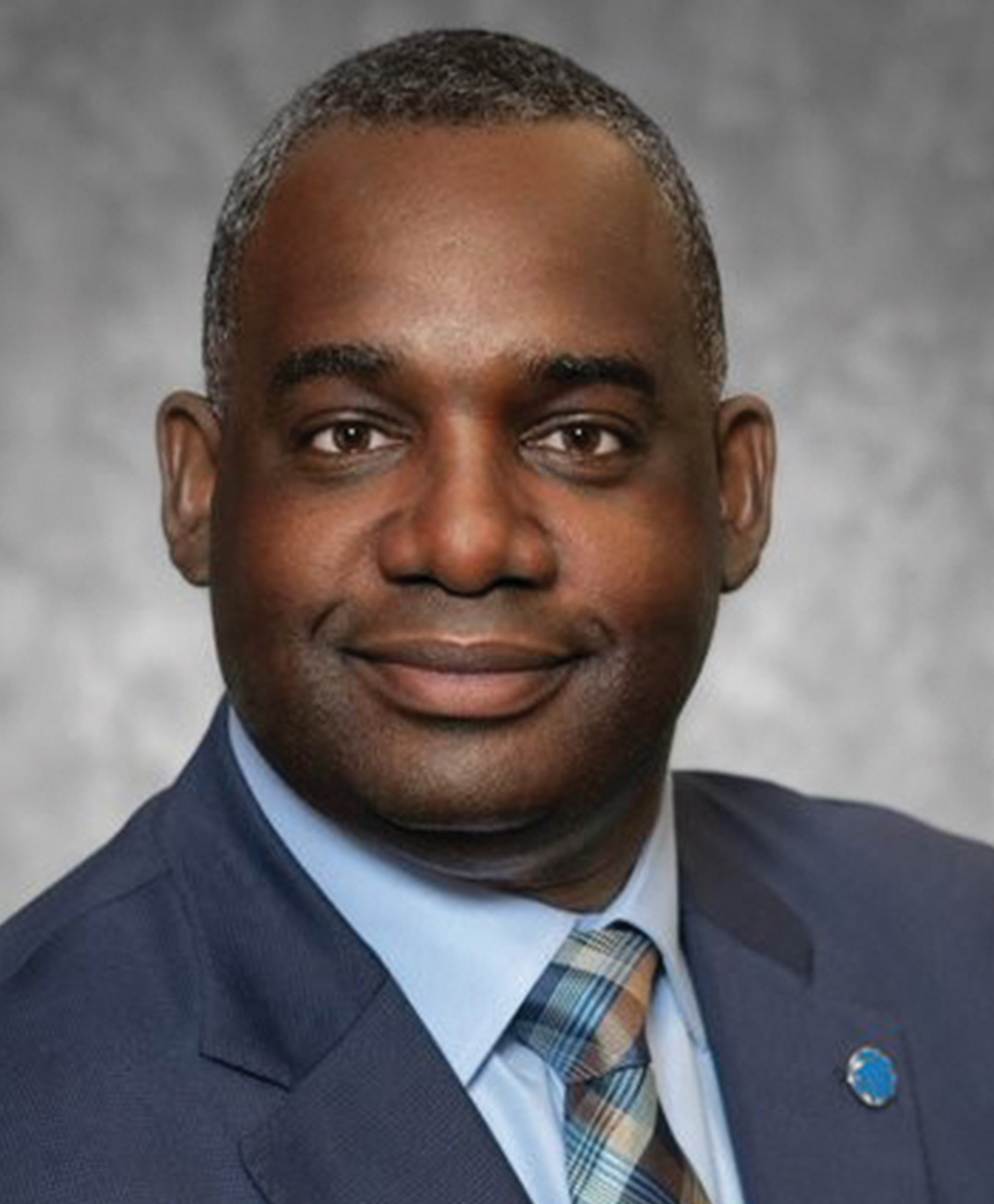
Craig Reed (MBA ’02)
Reed and his team immediately aligned with other internal functions to focus on the resilience of the company’s supply chain — identifying and addressing any risk to ensure operations could continue. The work required prioritization, agility, and close relationships with suppliers. It also required seamless engagement with internal business stakeholders.
“All of these challenges required a greater level of transparency, a greater level of collaboration, because the supply chains would change so quickly,” he says. “We needed to make sure we kept the lines of communication open.”
Collaboration was already part of the culture at Corteva but, moving forward, Reed expects the integration across sales, operations, procurement, manufacturing, and other teams will only get tighter.
“The value of the teams working cross-functionally, taking away the white space between the organization so that you can move a lot faster, has been critical to allowing us to deliver,” he says. “That’s how we are successful.”
Disruptions are a given in supply chain management. What set the COVID-19 pandemic apart was the level of uncertainty that followed.
“Disruptions can happen due to either ‘known unknowns’ or ‘unknown unknowns,’ ” says Srimathy Mohan, associate professor of supply chain management. “How do we distinguish between these two? It’s based on the predictability of the occurrence — its frequency, the magnitude and impact of the disruption, and the time it takes to recover.”
Take natural disasters like hurricanes and tornadoes: They’re often recurring and can be predicted with a fair amount of accuracy. But the magnitude and recovery are dependent on the strength of the hurricane, which can’t truly be understood until it makes landfall. Even the Texas freeze this past winter was relatively predictable — but the burst pipes and fallen power lines weren’t.
With unknown unknowns, however, nothing is predictable.
Mohan says health events typically fall in this category. However, there’s still a reasonable understanding of what to expect: a prevalent flu strain is identified, vaccines are produced, and supply chains ramp up during the annual flu season. Diseases such as avian flu and Ebola virus are progressively less predictable, but the impact is typically localized.
COVID-19, however, quickly reached pandemic status and the whole world essentially shut down. Multiple waves with hard-to-predict recovery times further complicated supply chain professionals’ ability to predict and manage the flow of goods.
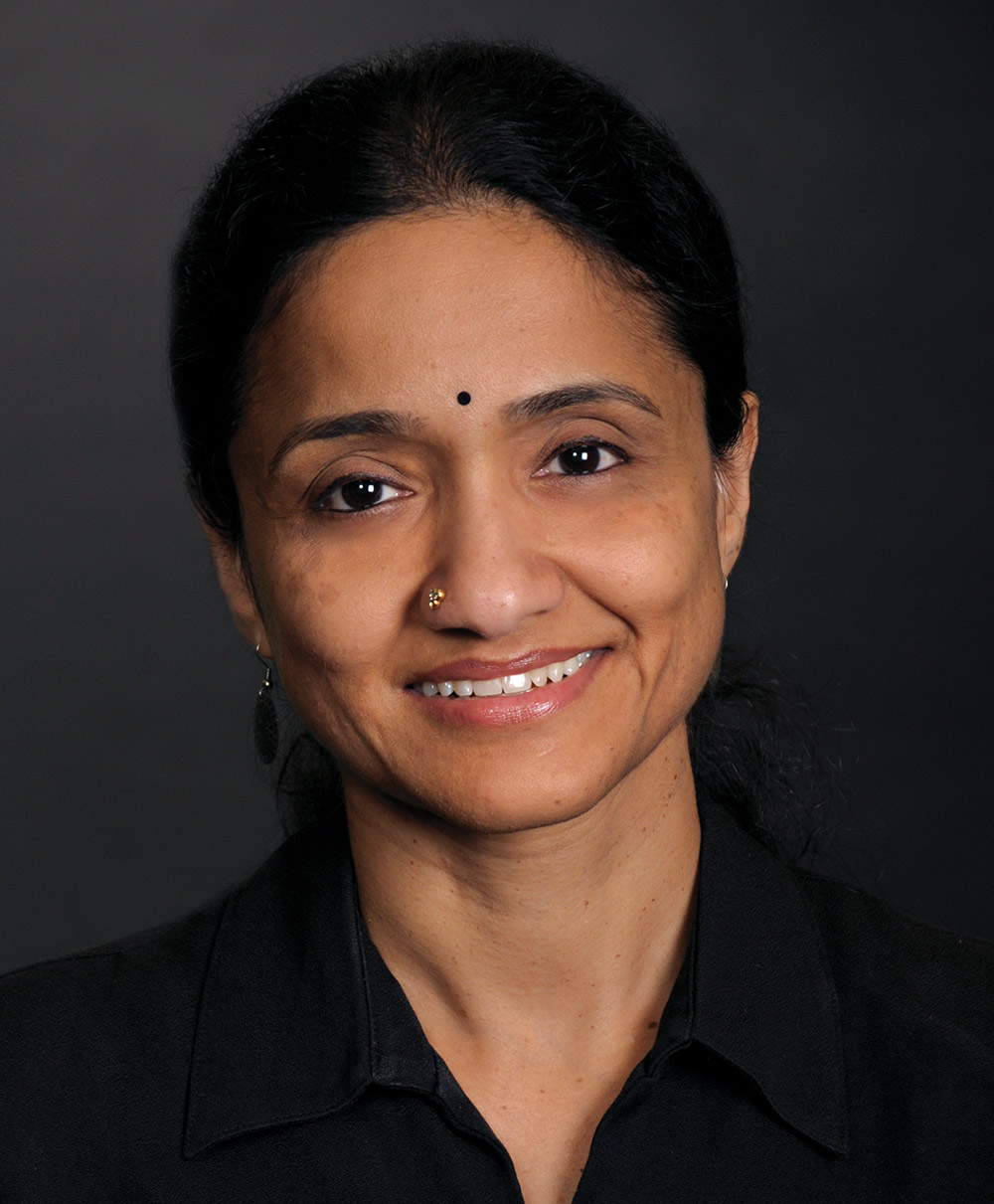
Srimathy Mohan
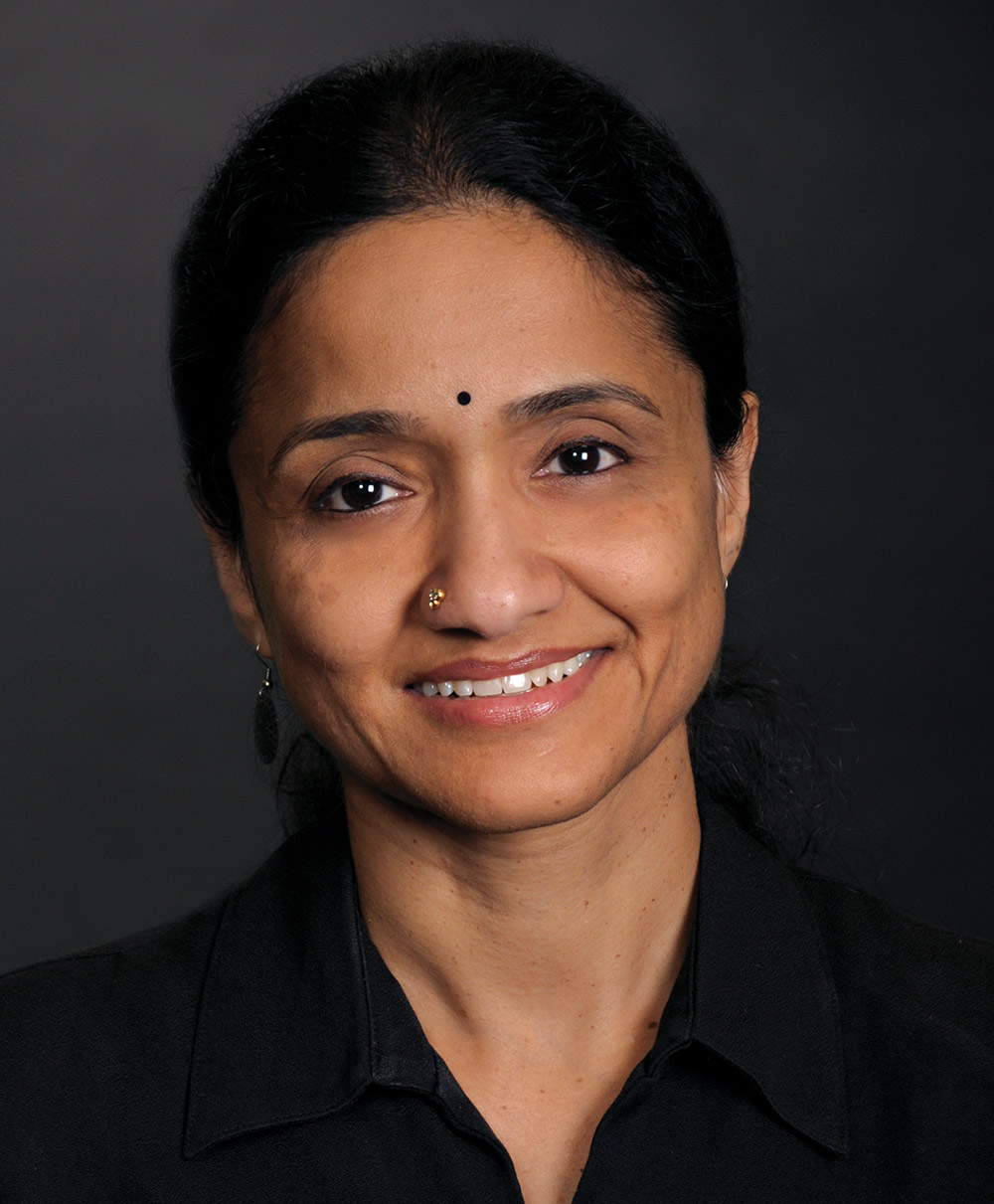
Srimathy Mohan
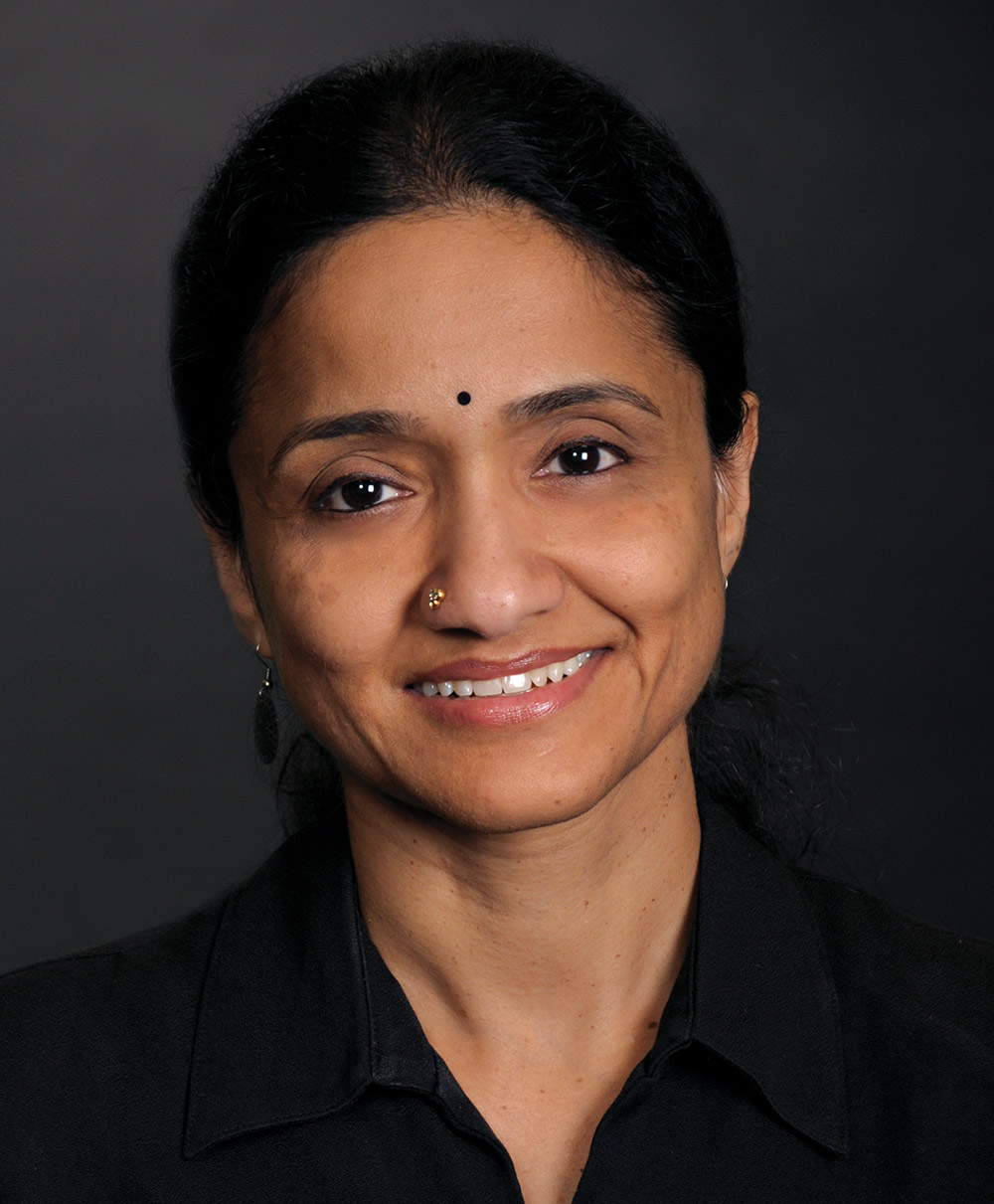
Srimathy Mohan
“It gives us another window to look at and start predicting things a little earlier in the future,” she says. “If something like this happens again, it could throw a different curveball at us, and we will roll with it as we learn more. But we all agree the yeast shortage is not an unknown unknown anymore.”
Whatever the next pandemic, natural disaster, or utterly unknown event throws at us, Mohan says it’s essential to take the information we’ve gleaned and develop a framework for handling future disturbances.
“When you encounter something new, you can quickly start mapping it onto a known classification,” she says. “Then you have tools that you can quickly adapt to something new that pops up. The idea is to hopefully have a basket full of known unknowns.”
Across industries, business leaders now see supply chain resiliency (see 3 types of supply network resiliency on p. 24) as not just responsible for on-time delivery and cost-savings but also critical to their work. In February 2021, President Joe Biden issued an executive order to strengthen American supply chain resiliency as a matter of national security and economic prosperity. Both Torrel and Puri say even their family members now understand their work — and the implications on their daily lives.
“When I thought about supply chain before,” Torrel says, “it worked in the background. It was a cost center. Everybody expected toilet paper on the shelf at any given time. It was important but maybe undervalued.
“Today, it’s critical. It’s moved to the forefront of a lot of people’s minds. Organizations, when they’re looking at what they need for success in the future, it’s an agile and resilient supply chain.”